UV DTF printing is a cutting-edge technology that is revolutionizing the digital printing industry. It offers high-quality prints with vibrant colors and exceptional detail, making it a popular choice for various applications. In this guide, we will explore the fundamentals of UV DTF printing, its pros and cons, the equipment needed, and the step-by-step process. Additionally, we will delve into some tips and best practices for achieving optimal results and discuss the wide range of applications for UV DTF printing
What is UV DTF Printing
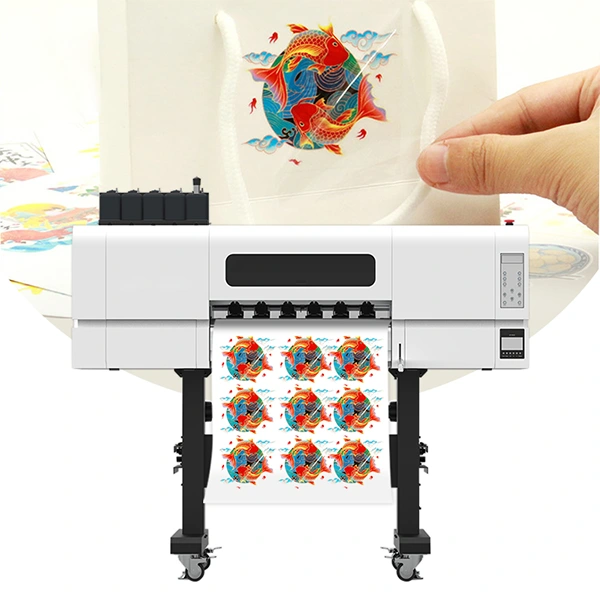
UV DTF printing, also known as UV Direct-to-Film printing, is a digital printing technique that uses UV curable inks to directly print designs onto a specialized transfer film. This film, coated with a release layer, allows the design to be easily transferred to a wide range of materials, including textiles, wood, glass, and metals.
What sets UV DTF printing apart from traditional printing methods is its ability to produce prints with exceptional detail and vibrant colors. Unlike other methods that apply ink layers on top of the material, UV DTF printing penetrates the surface, resulting in a more durable and long-lasting print. The UV curable inks used in this process cure instantly when exposed to ultraviolet light, creating a strong bond with the substrate.
UV DTF vs DTF
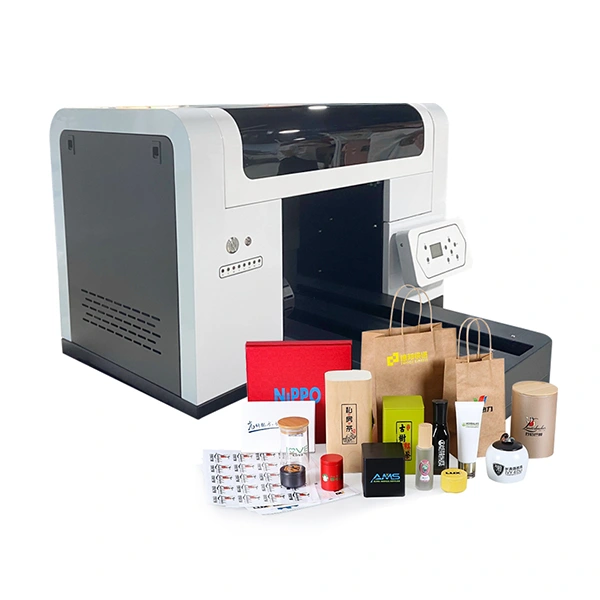
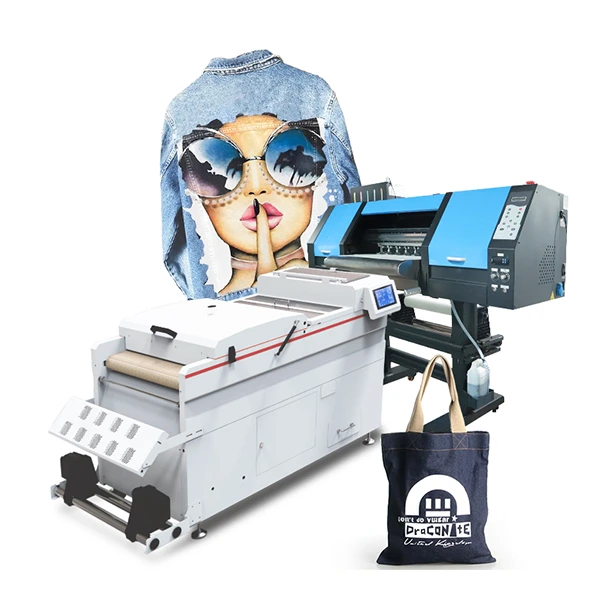
The key difference between UV DTF and DTF (Direct-to-Film) printing lies in the inks and curing processes used.
In UV DTF printing, UV curable inks are used, which cure instantly when exposed to ultraviolet light. This curing process provides excellent durability, vibrant colors, and resistance to fading and abrasion. UV DTF printing allows for printing on various materials and offers faster production times compared to DTF.
On the other hand, DTF printing utilizes water-based inks that require heat and pressure for transfer. The design is printed onto a film, which is then transferred onto the substrate. DTF printing also provides vibrant colors but may not offer the same level of durability as UV DTF prints.
Overall, UV DTF printing offers higher durability and faster production times, while DTF printing can be a cost-effective option for smaller-scale operations. The choice between the two depends on factors such as desired print quality, durability requirements, and budget considerations.
Pros and Cons of UV DTF Printing
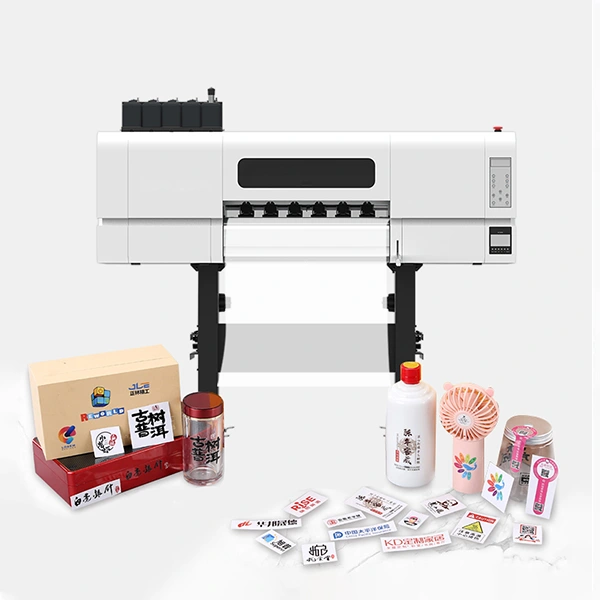
Advantages of UV DTF Printing
- High print quality and vibrant colors: UV DTF printing offers exceptional print quality with crisp details and vibrant colors. The UV curable inks used in this process have a wider color gamut, allowing for accurate color reproduction.
- Versatility in printing on various materials: UV DTF printing can be applied to a wide range of materials, including fabrics, plastics, ceramics, and metals. It is a versatile printing technique that opens up endless possibilities for customization.
- Faster production time compared to other methods: UV DTF printing is known for its fast production time. The UV curable inks dry instantly when exposed to ultraviolet light, eliminating the need for drying time and allowing for quick turnaround.
Disadvantages of UV DTF Printing
- Cost factors and initial investment: UV DTF printing requires specialized equipment, including a UV DTF printer, UV curable inks, and coatings. The initial investment can be high, making it less accessible for small-scale businesses.
- Limitations in printing fine details and gradients: While UV DTF printing offers exceptional detail, it may have limitations when it comes to printing fine details and gradients. The thickness of the UV curable inks can affect the smoothness of gradients, requiring additional techniques for achieving desired results.
- Requires specialized equipment and expertise: Operating a UV DTF printer requires specialized knowledge and expertise. Proper maintenance and calibration are essential for consistent print quality. Additionally, understanding RIP software and color management is crucial for achieving accurate color reproduction.
What do I Need for UV DTF Printing
To embark on your UV DTF printing journey, you will need the following equipment and materials:
UV DTF printer
This specialized printer is designed to handle the UV curable inks used in the DTF printing process. It is equipped with advanced features for precise printing and UV curing.
UV curable inks and coatings
UV curable inks are specifically formulated to cure instantly when exposed to ultraviolet light. These inks offer vibrant colors and excellent adhesion to various substrates. UV coatings are applied to enhance the durability and finish of the prints.
UV DTF Transfer film and release paper
The UV DTF transfer film acts as a carrier for the design during the printing process. It is coated with a release layer that allows for easy transfer of the design onto the desired substrate. Release paper is used to protect the printed UV DTF transfer film during storage and transportation.
Laminator
A laminating machine is used to transfer the printed design from the UV DTF transfer film onto the desired substrate. It ensures proper adhesion and eliminates air bubbles, resulting in a seamless transfer.
Step-by-Step Process of UV DTF Printing
- Design with RIP software on the computer and place the adhesive side of UV DTF A film on the platform of the UV DTF printer.
- Prefill the cartridge with CMYK ink, white ink, and varnish to print your design on the UV DTF A film.
- Use the laminating machine along with the UV DTF Printer to transfer the pattern on B film.
- Peel off the A film of the pattern and stick it on the item you want to print. Then slowly peel off the B film, and your product is finished.
Tips and Best Practices for UV DTF Printing
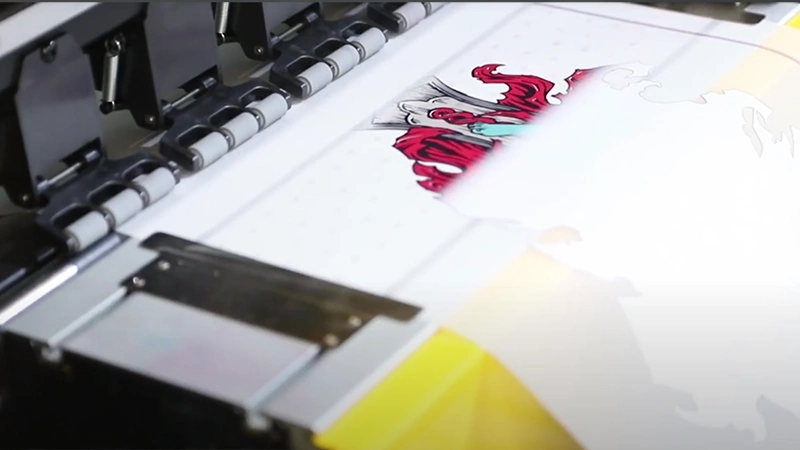
To ensure the best possible results and optimize your UV DTF printing experience, consider implementing the following tips and best practices:
Selecting the Right Substrate for Optimal Results
Choosing the appropriate substrate is crucial for achieving optimal print quality. Different materials have different surface properties and compatibility with UV DTF printing. Experiment with various substrates to find the ones that yield the best results for your specific designs. Consider factors such as texture, absorption, and color to ensure the desired outcome.
Proper Maintenance and Care of UV DTF Printer
Regular maintenance and care are vital for the longevity and performance of your UV DTF printer. Follow the fabric printer manufacturer’s guidelines for cleaning procedures, preventive maintenance, and calibration. Keep the printer in a clean and dust-free environment to avoid any contamination that could affect print quality.
Testing and Experimenting with Different Settings and Techniques
UV DTF printing offers a range of customization options and effects. Take the time to experiment with different settings, such as ink densities, curing times, and print resolutions. Test various techniques to achieve the desired finishes, gradients, and textures. Keep a record of your settings and results for future reference.
Post-processing and Finishing Options for Enhanced Durability
Consider post-processing and finishing options to enhance the durability and aesthetics of your UV DTF prints. Applying a protective coating or varnish can improve resistance to abrasion, UV fading, and chemical exposure. Depending on the substrate, you may also explore additional techniques such as heat pressing or embroidering to add dimension and texture to your prints.
Optimizing RIP software and Color Management
RIP software plays a crucial role in color management and print accuracy. Ensure your RIP software is calibrated and profiles are set up correctly. Use color swatches and spectrophotometers to verify color accuracy and consistency. Regularly update your software to benefit from the latest features and improvements.
Application of UV DTF Printing
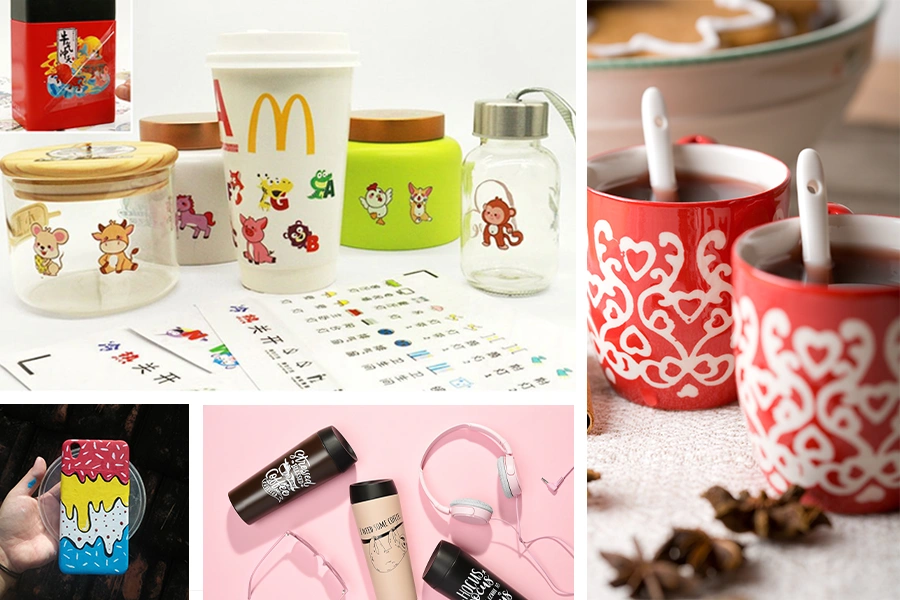
UV DTF printing finds applications in various industries due to its versatility and high-quality results. Some common applications include:
- Garment and apparel industry: UV DTF printing is widely used for printing on t-shirts, hoodies, and other fabric items. It offers the ability to print vibrant designs with exceptional detail, making it a popular choice for customization.
- Home decor and personalization: In the home decor industry, UV DTF printing allows for customizing home textiles, cushions, and canvas prints. It offers endless possibilities for personalized designs and creates unique decor items.
- Promotional and marketing materials: UV DTF printing is an excellent choice for creating eye-catching banners, posters, and promotional items. The vibrant colors and high print quality make the designs stand out, leaving a lasting impression on potential customers.
- Industrial and commercial applications: UV DTF printing can be used on rigid materials like wood, glass, and metals. It opens up opportunities for customization in the industrial and commercial sectors, including signage, labeling, and product decoration.
Conclusion
UV DTF printing is a game-changer in the digital printing industry, offering high-quality prints with vibrant colors and exceptional detail. Its versatility in printing on various materials, combined with faster production time, makes it an attractive option for businesses and individuals alike. With the right equipment, materials, and expertise, UV DTF printing presents endless opportunities for customization and creativity. Embrace this technology and explore the boundless potential it holds in the world of digital printing.